Belt Conveyor

As standard design, plastic scraps such as film, filament, raffias conveyed into the compacting room through belt conveyor; to handle rolls’ scraps, roll hauling off device is an optional feeding method. Motor drives of conveyor belt and hauling device cooperate with ABB inverter. Feeding speed of conveyor belt or roll hauling off is fully automatic based on how full the compactor’s room is.
Metal Detector

Optional Ferrous Metal Permanent Magnetic Belt or metal detector can prevent metal specials from entering the crusher and effectively protect the blades of the crusher.
Rotor
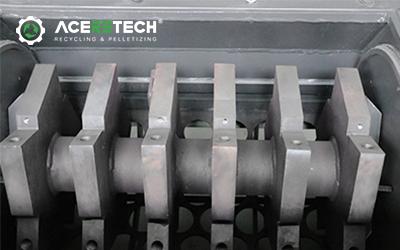
Heavy-duty vane rotor, welded steel structure, with rotary knives, V-shaped mounting angle, and X-shaped cutting shape. The extension shaft of the rotor can be equipped with a governor wheel. The adjustable rotor tool minimizes the downtime of tool change.
Knife Blades
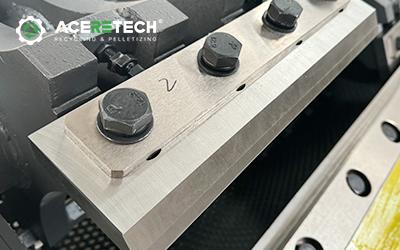
Knife Blades Material: DC53 Higher hardness (62-64 HRc) than D2/SKD11 after heat treatment; Twice the toughness of D2/SKD11 with superior wear resistance; Substantially higher fatigue strength compared to D2/SKD11.
Crushing Chamber
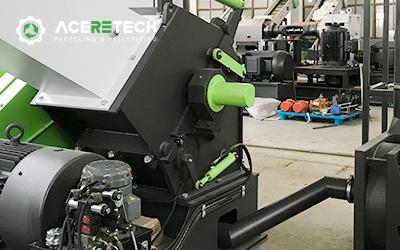
The crushing chamber is welded with 40mm ultra-high hardness steel plate, which is wear-resistant, corrosion-resistant, low-noise, and has a longer service life.
Motor

Adopt imported brand motor WEG, low energy consumption, low noise, long service life.
Frame
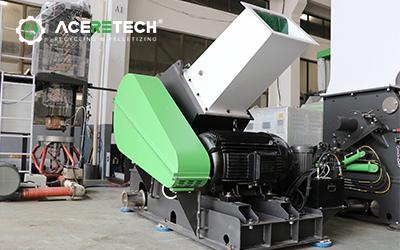
Welded structure, the whole frame is placed on the shock-resistant rubber-metal connector, which can resist shock and reduce noise.
Silo
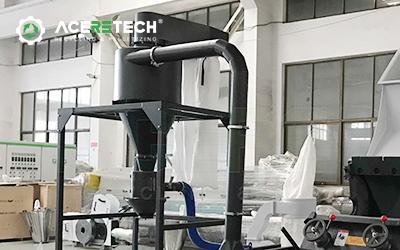
Adopts a large air volume and silent air supply system. The pipes and silos are made of 304 stainless steel, and the exterior is covered with sound insulation cotton, which can effectively reduce noise.
Electronic Control
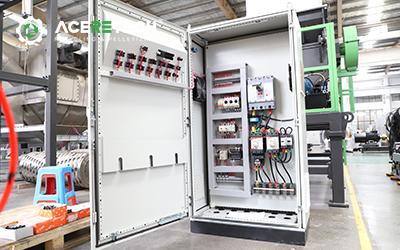
The whole model adopts frequency conversion control and conforms to international standards such as CE/CSA.
Tool Installation

The tool can also be adjusted while the equipment is running, reducing equipment downtime.The tool can also be adjusted while the equipment is running, reducing equipment downtime. The tool can be quickly adjusted outside the machine, which minimizes downtime and makes tool replacement easier.The tool can be quickly adjusted outside the machine, which minimizes downtime and makes tool replacement easier.