Belt Conveyor
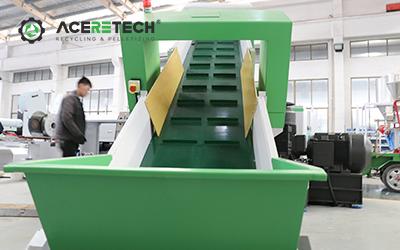
The plastic waste is conveyed into the shredder through the belt feeding device; * The device adopts ABB/Schneider frequency converter for frequency control. * The conveying speed of the belt feeding device is linked with the fullness of the shredder, and the speed of the conveyor belt is automatically adjusted according to the current of the shredder.
Metal Detector

Optional Ferrous Metal Permanent Magnetic Belt or metal detector can prevent metal specials from entering the shredder and effectively protect the blades of the shredder.
Hopper
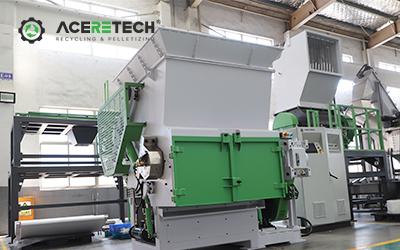
Special designed hopper to avoid material flying out. The machine is fitted with a large filling hopper and can be loaded by conveyor belt, fork lift, crane or wheel-loader. This funnel can be adapted to suit individual requirements and guarantees a continuous and economical supply of material.
Hydraulic Ram
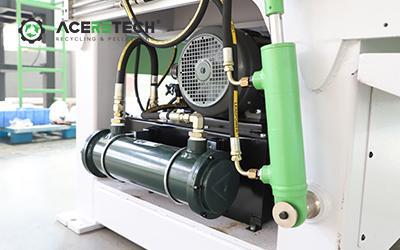
The hydraulically operated pusher feeds the material towards the cutter automatically by load-related controls. The hydraulic system is equipped with overflow valves and volumetric flow controls, which can be both set according to the demands of the input materials.
Rotor
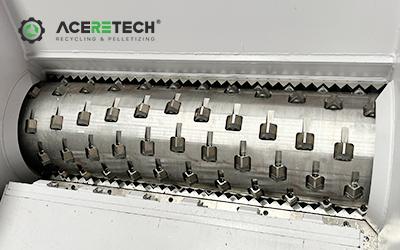
The profiled rotor made of full solid steel has wide diameter and operates at proper speed The concave ground, aggressive and 4-way rotating knives are mounted in the grooves of the profiled rotor with special knife holders. This enables a reduction of the cutting gap between the counter knives and the rotor and guarantees a high flow rate, low power consumption and maximum output of ground material.
Knife Blades Knife
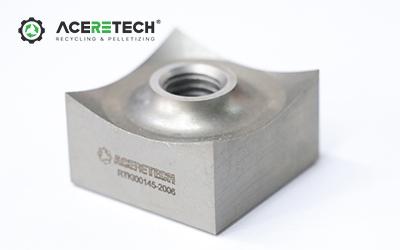
Blades Material: DC53 Higher hardness (62-64 HRc) than D2/SKD11 after heat treatment Twice the toughness of D2/SKD11 with superior wear resistance Substantially higher fatigue strength compared to D2/SKD11
Screen
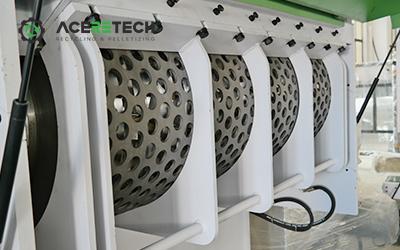
The screen mounted beneath the rotor determines the size of the required flakes. The screen is also easily accessible by a separate flap and can be changed easily. The screen can be opened or closed hydraulically.
Shredder Chamber
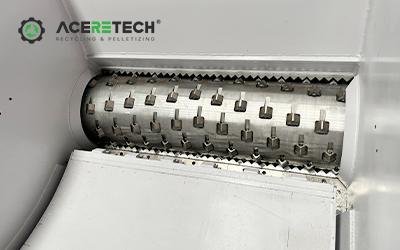
The shredder chamber is welded with 30mm ultra-high hardness steel plate, which is wear-resistant, corrosion-resistant, low-noise, and has a longer service life.
Motor
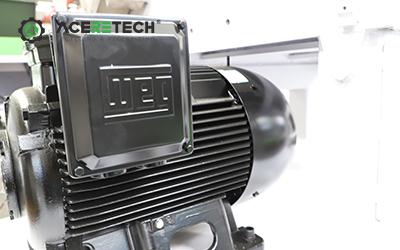
Adopt imported brand motor WEG, low energy consumption, low noise, long service life.
Electronic Control
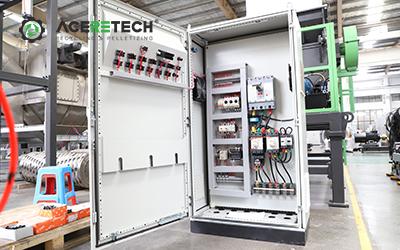
The whole model adopts frequency conversion control and conforms to international standards such as CE/CSA.
Tool Installation
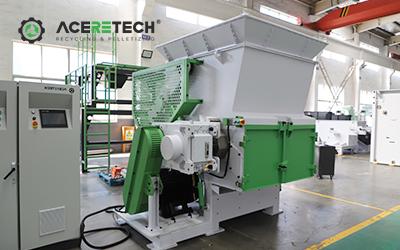
The tool can be quickly adjusted outside the machine, which minimizes downtime and makes tool replacement easier.