物料运输
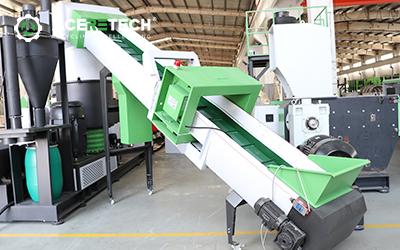
上料
标准设计,薄膜、长丝、拉菲草等塑料废料通过皮带输送机输送到压实室;为处理卷料边角料,可选配卷料牵引装置。传送带和牵引装置的电机驱动与 ABB 变频器配合使用。传送带的进给速度或辊牵引的速度是全自动的,取决于压路机房间的装满程度。
金属探测仪可与皮带输送机结合,与控制系统联锁,在进料时发现金属时发出警告和停止系统。
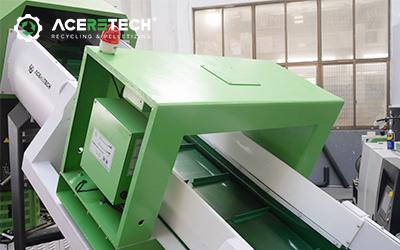
金属探测器
金属探测器可以与皮带输送机结合使用,并与控制系统联锁,如果在进料中发现金属,则发出警告并停止系统。
碎和压实
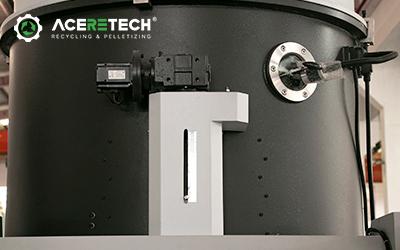
伺服电机推拉门
它可以处理硬质和软质材料。滑动闸门控制物料在压实机内的停留时间,达到预干燥的效果,保证干净干燥的物料进入筒体。达不到处理效果的材料将无法进入下一道工序。 PLC精确控制强制进料量,确保产能。
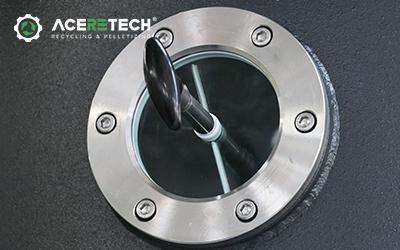
高亮度灯筒
配备高亮度灯筒,专为查看压实舱内物料情况而设计。该灯筒采用高品质LED灯珠,光线均匀且亮度十足,操作人员可以直观地观察到物料在压实舱内的分布情况,及时调整喂料速度和压实程度,确保造粒过程的顺畅进行。此外,灯筒的外壳采用防护等级高的材料制成,有效防止粉尘和水分侵入,保证了灯筒的长期稳定运行。
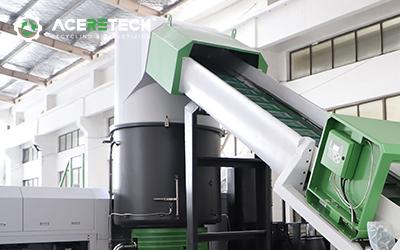
压实仓
刀盘上的旋转刀片和壁上的固定刀片将塑料材料切成小片。高速摩擦产生的热量对片料进行预热和干燥,使其收缩。
弧形板在刀盘的离心力作用下将物料向下引导到挤出机。
这种破碎、预热和压实的组合过程使小体积密度的塑料能够稳定有效地进料。
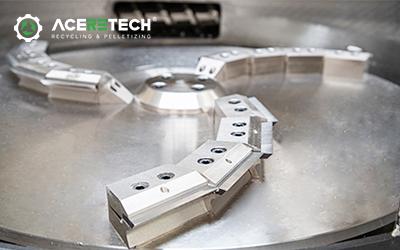
压实机的旋转叶片
旋转刀片和固定刀片将物料切成小片。高速旋转的叶片产生的摩擦热会使薄片过热并收缩。
配有排气装置压实机
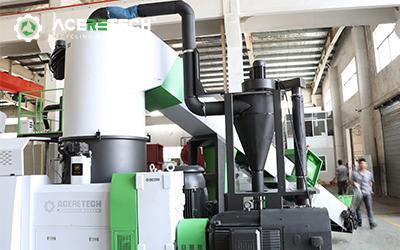
压实机配有排气装置
压实机设有抽风装置,随着压实机底部动刀、定刀的机械工作,经过不断的切割、摩擦,压实机和物料的温度逐渐升高,原料表面的水分和灰尘会浮到压实机的顶部,该装置能有效去除水分和灰尘,避免使用额外的能耗来处理水分。从而在造粒前对物料进行进一步的干燥。干燥减少了后道装置处理塑料水分的压力,从而提高了作业效率,提高了产品质量。
单螺杆挤出机
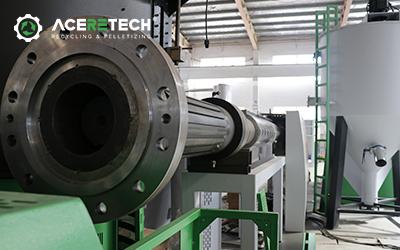
机筒
由于超长的长径比,生产线中的单级挤出机可作为双级挤出机使用。在中间的双活塞式筛网过滤器之后,可以在最后增加一个过滤器。双重过滤标准可以提高最终产品颗粒的质量和性能。
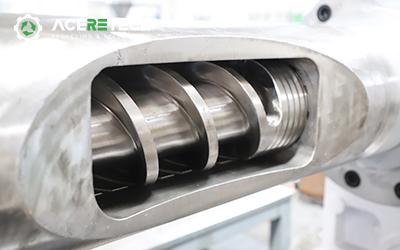
单螺杆挤出机
我们独特的设计单螺杆挤出机温和地塑化和均化材料。我们的双金属挤出机具有很好的防腐、耐磨和长寿命。
双真空脱气区
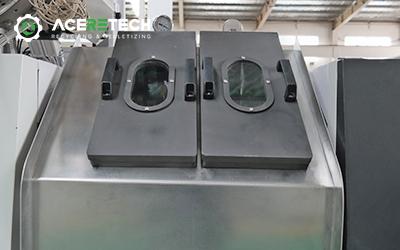
双真空脱气区
双真空脱气区,有效去除小分子、水分等挥发物,提高颗粒质量,特别适用于厚重印刷品。
过滤系统
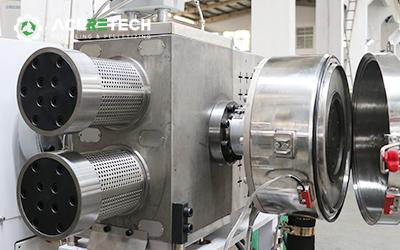
- 挤出机机头可安装常规单板/活塞双工位换网器或不停机双板/活塞四工位,过滤性能显着。
- 滤网寿命长,滤网更换频率低:过滤面积大,滤网寿命长
- 使用方便不停机型:换网方便快捷,无需停机。
- 非常低的运营成本。
不停机活塞式过滤器
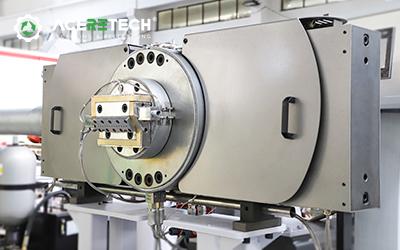
板式过滤器
板式过滤器由两个过滤板制成连续式。换网时至少有一个过滤器在工作。环形加热器,加热持续稳定。
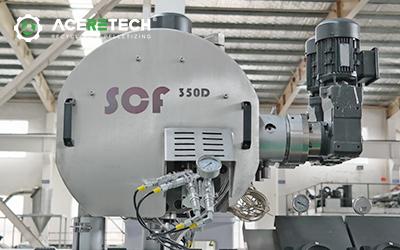
自清洁过滤器
该机型结合了我公司自主研发的自清洗过滤器。全新的SCF自清洗过滤系统,实现不停机回收挤压,特别适用于高污染物料的再造粒。 SCF 过滤系统可以处理和去除熔体流动中高达 5% 的污染物,可以将污染物分离为:纸张、木材、铝、未熔化的塑料和橡胶等。
造粒系统
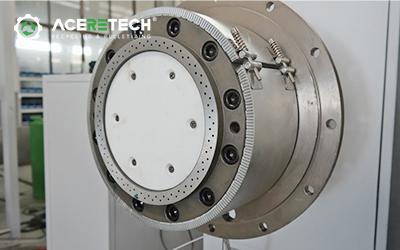
模头
对于需要更好的熔体过滤和更高的产量来说,这是最合适的工艺。在第一阶段,可以为两阶段造粒生产线设计两台或多台单螺杆挤出机,然后它们可以同时进入第二阶段挤出机。
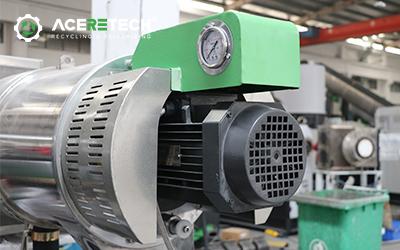
水环造粒系统
- 由于刀片压力始终正确,因此自调节制粒头可以获得最佳的颗粒质量并延长正常运行时间。
- 旋转叶片的转速是根据熔体挤出压力自动进行的。
- 切粒机刀片更换方便快捷,无需调整工作,节省时间。
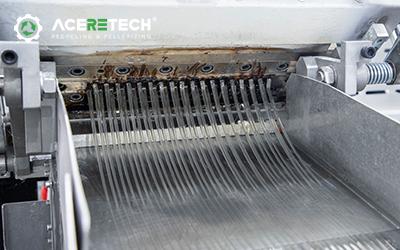
拉条切粒
条状的熔融塑料线材通过冷却水槽,迅速冷却固化。在冷却过程中,条带由牵引装置拉出,保持一定的速度和稳定性。然后,条带进入切粒机,由旋转的切刀切成一定长度的颗粒。
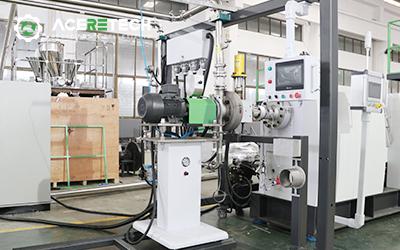
水下造粒系统
高度自动化的制粒系统。适用于高MFI和高生产能力要求的材料。该系统包括制粒机、阀门、输送管道、脱水振动筛、料仓。
振动干燥

振动干燥
- 先进的脱水振动筛结合卧式离心脱水,干燥颗粒性能高,能耗低。
- 组装筛网:筛网采用螺丝安装固定,无需焊接,方便日后更换筛网。
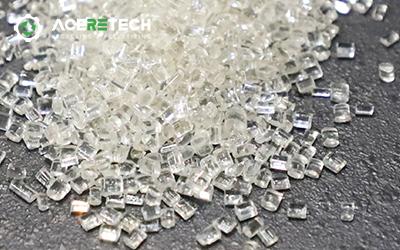
塑料颗粒
最终输出:塑料颗粒,塑料颗粒可再次用于生产高质量的塑料制品
包装系统
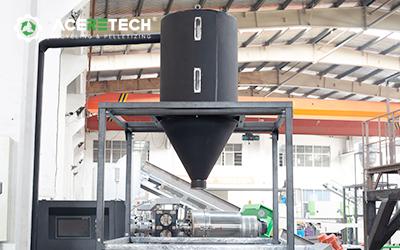
包装系统
- 最终合格的颗粒在这里存放,干燥摇床配合卧式离心机干燥效果好,能耗低。
- 容量在线监测和定量称重系统。
智能控制
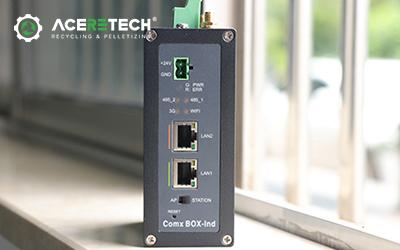
远程监控和信息传输
系统程序远程监控和传输系统,蓝牙均可用于ACS系统实现远程监控和信息传输功能。
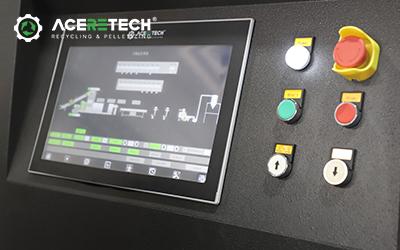
智能控制
智能启动:一键启动 按照设定的物流顺序和物料处理要求,联锁系统模块可以“一键启动” 智能停止:一键启动 ACS系统中的每个相关模块部件都可以一键关闭。紧急停止ACS系统具有紧急停机功能,以防机器运行过程中出现不确定风险。
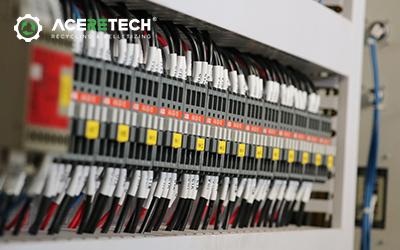
欧洲电气
电气设备精选欧洲品牌电器元件,确保设备在运转过程中的高效与安全。
设备配电系统设计合理,线路布局清晰,有效降低了故障率。