LSP PET Plastic Recycling Machine Line With Liquid State Polymerization System For IV Improvement
LSP Pet Plastic Recycling Machine Line With Liquid State Polymerization System For IV Improvement
The Aceretech LSP Series is a PET Plastic Recycling Pellet Line equipped with innovative technology that uses Liquid State Polycondensation (LSP) to transform PET scrap or flakes into valuable products in a very short time. Whether you want to recycle bottle to bottle, fiber to fiber, or make PET fiber, packaging strip, pellet, or film, the LSP Series can do it all with a fully controllable iV value and absolute process stability. It is a PET recycling solution that can handle various materials, produce high-quality plastic granules, and save energy and costs.
The LSP Series is the best choice for every PET recycling factory that wants to improve the recycling utilization and quality of resources. Contact us today to find out more about the Aceretech LSP Series and how it can revolutionize your PET recycling process!
Recycling & Material
LSP Pet Plastic Recycling Machine Line With Liquid State Polymerization System For IV Improvement
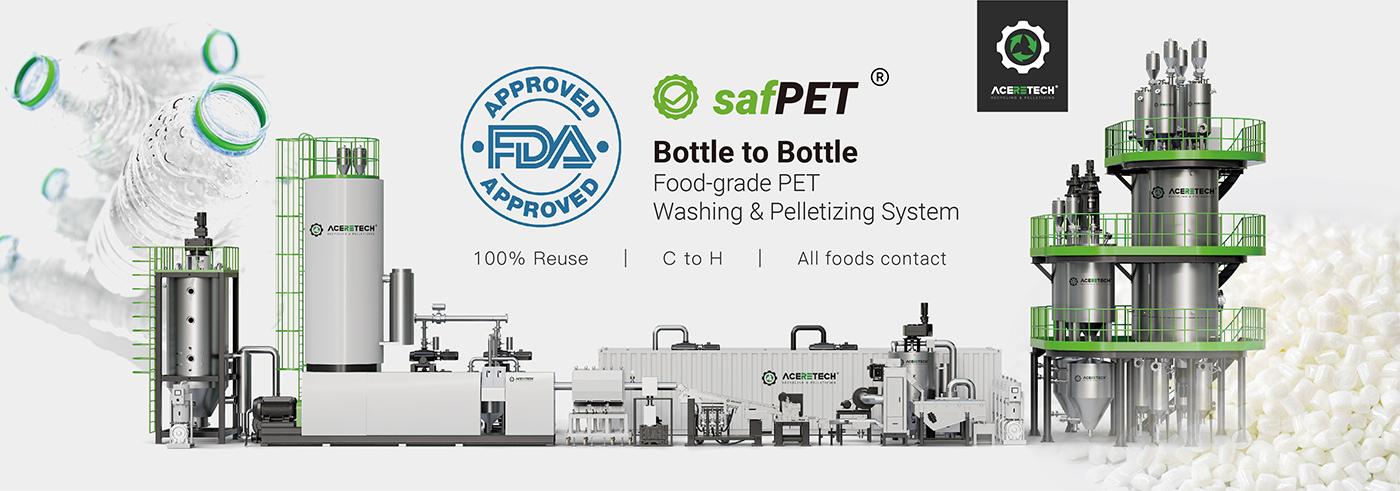
LSP (Liquid State Polycondensation) improve the quality of PET recycling material (fibre, bottle flake, film, Low IV polymer) , To produce high grade PET fibre, PET packaging strip, PET pellet, PET film, Recycle bottle to bottle, fibre to fibre, improve the recycling utilization and quality of resources.
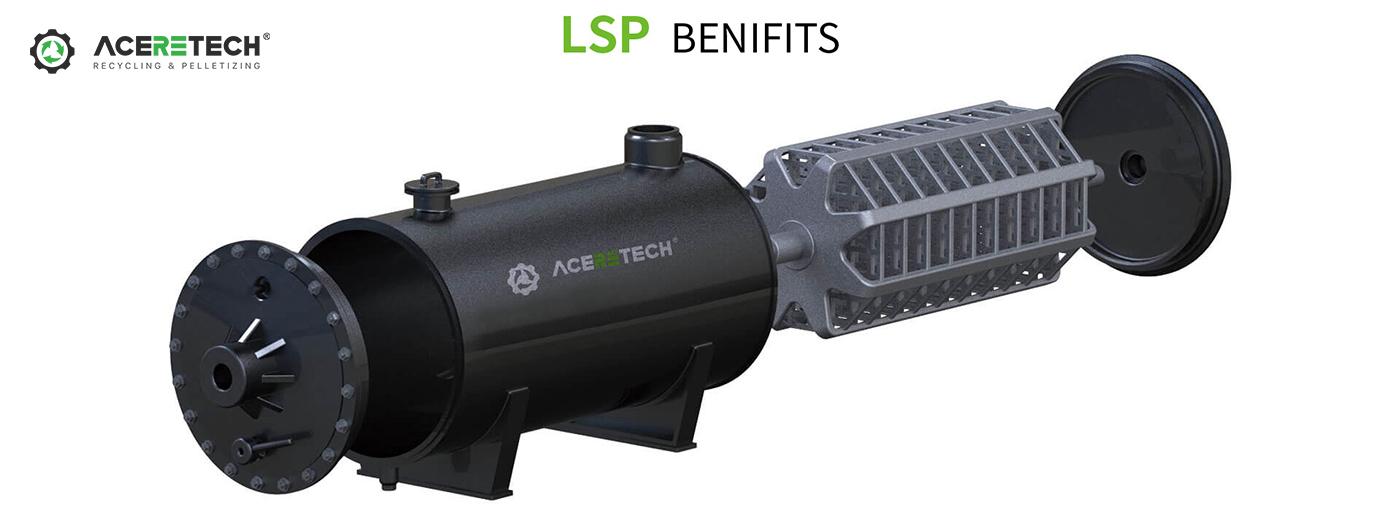
Innovation structure
The innovative structural design of the reactor, increases the reaction area of polymerization, improves the fluidity of PET melt, makes the reaction time shorter.
Smart Control
With our new smart control system, operations and real-time monitoring is more convenient than ever before, to predict maintenance and improve production efficiency.
High Energy Efficiency
Frequency conversion equipment is used to automatically adjust operation frequency. The multiple level temperature control system minimizes the required heating energy consumption and reduces the operation cost of the whole system.
LSP Excellent IV improvement effect
With our good homogenization feature, the reactor could mix different raw materials into homogeneous melt.
Applicable materials
PET film, sheet, waste, perforated waste, or fabric fibers, polyester fabric, and waste yarn, etc.
Through the buffer of our reactor, the whole production system is more controllable, increase output and avoid time lost during the process of replacing filters.
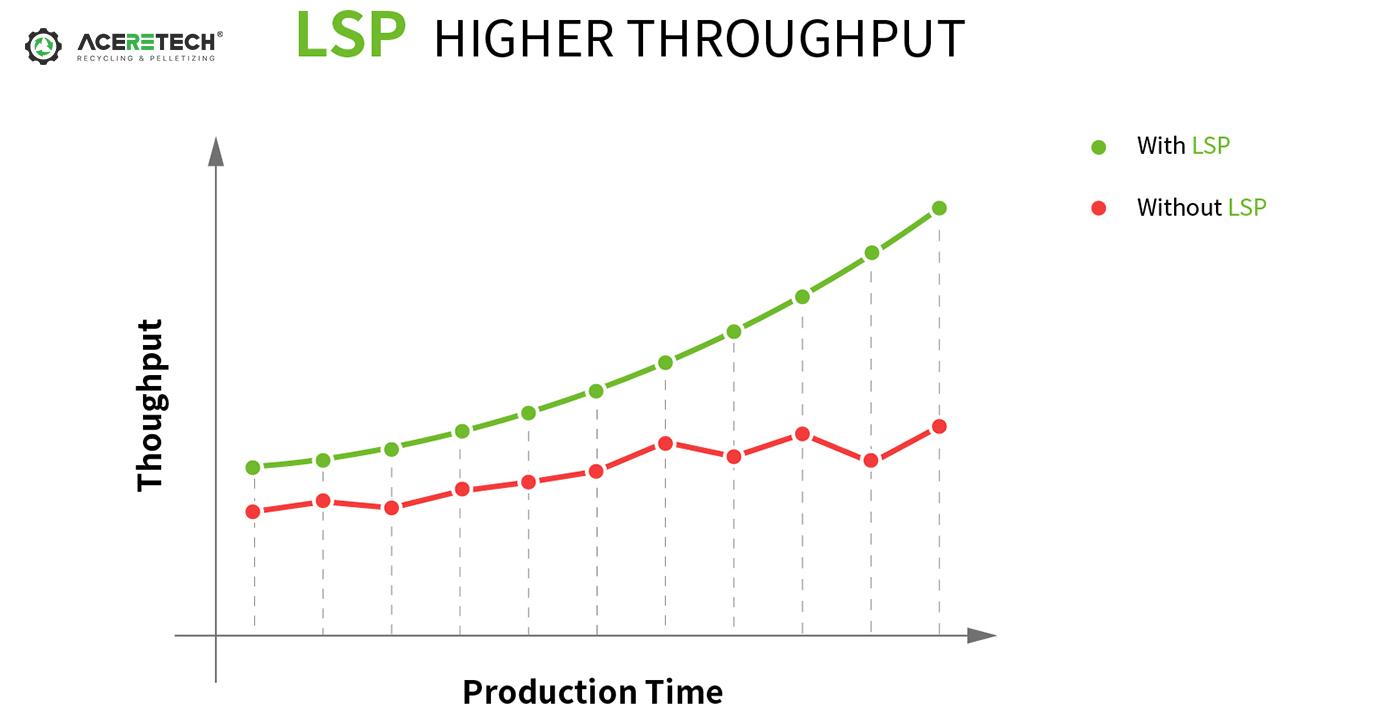
LSP is an extremely efficient alternative to a Solid State Polymerization (SSP) as there is no energy needed to cool the polymer down and then reheat it. Further, the reaction time in the melt phase is considerably faster than in the solid phase, which also contributes to the better economics of the LSPLINE™ system.

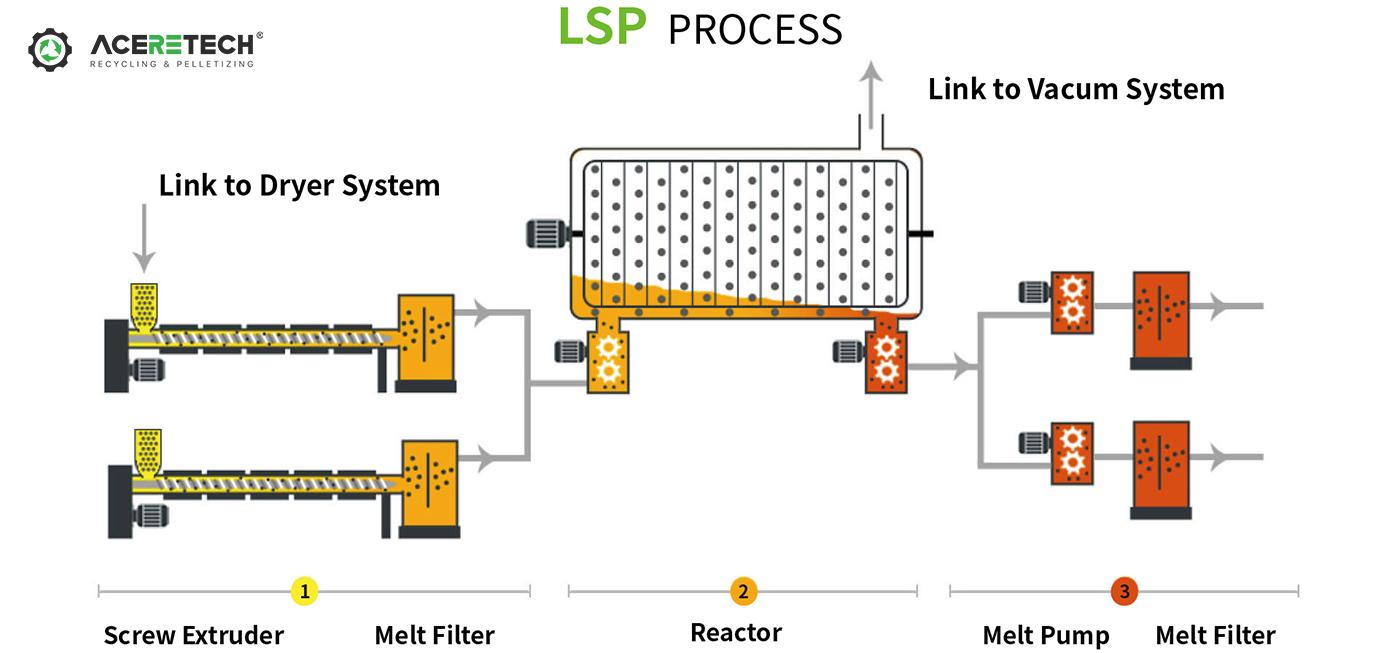
Because the source of recycled material is complex, the components are difficult to guarantee, which shows that the fluctuations of melt in production process. In order to stabilize the IV, the reactor runs at a certain speed, so that the internal melt is fully mixed.
Remove Impurity
Because PET re-polymerization is carried out in a high vacuum state, the low molecular material contained in the raw material and the auxiliaries will be vaporized in high temperature.
Molecular Chain Growth
There are still a large number of hydroxyl and carboxyl molecules in the raw materials, and the catalytic system is still effective. the polymerization still occur under certain temperature and vacuum state, The molecular chain and IV will increase.
LSP Multiple Filter System
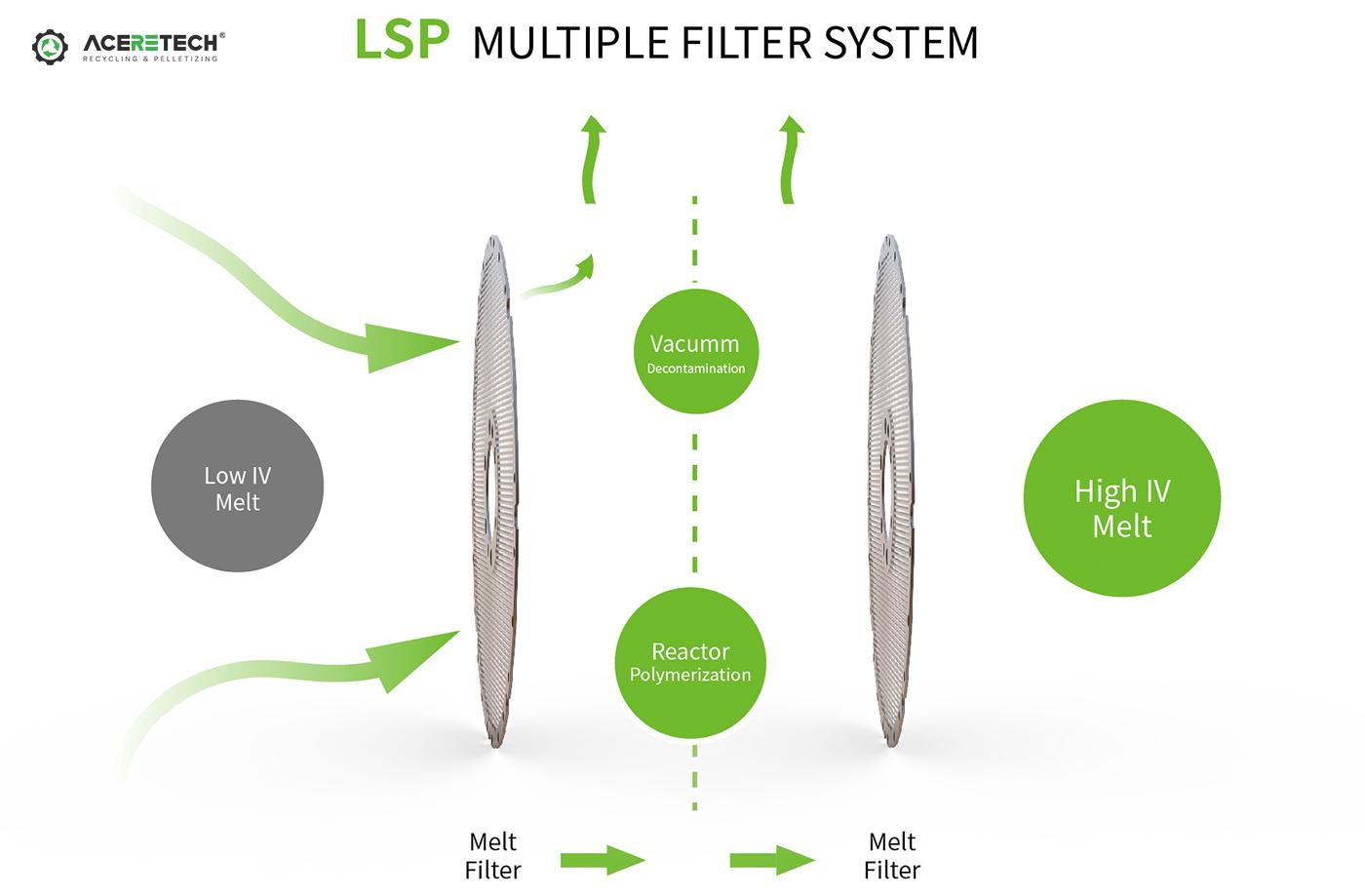
The first melt filter after the extrusion can filter the inorganic impurities, and facilitate the further reaction.
During Reaction
Under high vacuum conditions, the oligomers and decomposed gases are separated from the melt and removed into the vacuum system.
After Reaction
High-viscosity melt passes through the last melt filter and the inorganic impurities that still remain in the melt will be filtered.
LSP High Quality Products
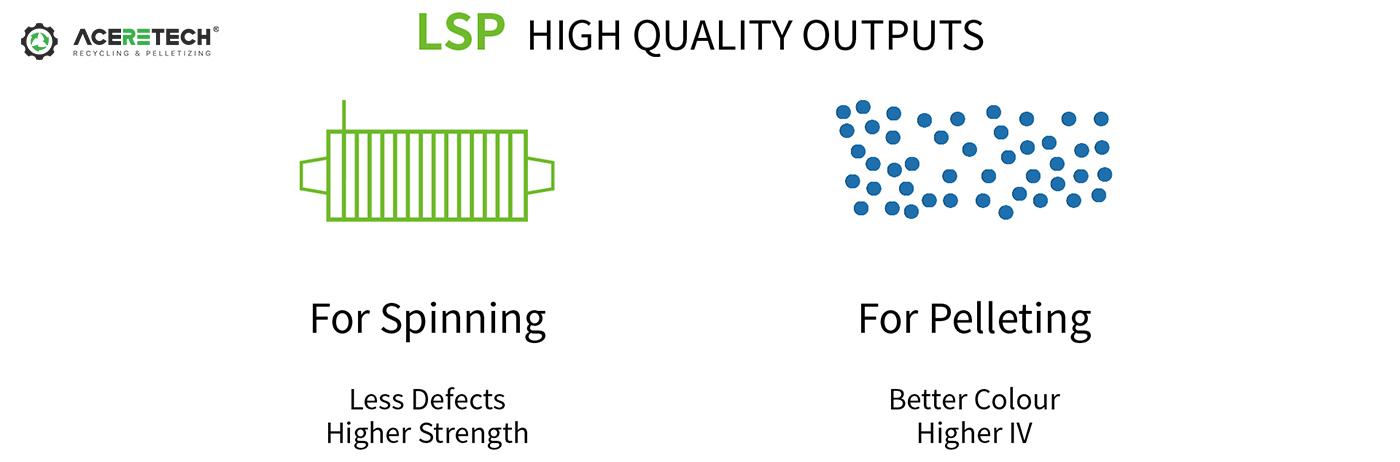
High Purity
After multiple filtration and homogenization, the recycled polyester melt has higher purity and IV, and color of the end product are more uniform.
High Strength
Under the high temperature and vacuum polymerization reaction, the molecular chains and IV are continuously increased, and the strength of the produced polyester product is also better.
LSP Reactor Innovation
The homogenization viscosity reactor has an internal structure similar to the final polymerization pot incontinuous polymerization units, both using horizontal polymerization pots. The internal structure of thehorizontal reactor can be divided into two types: disc-shaped and cage-shaped. Disc-shaped reactors havea smaller surface area and lower film formation efficiency, with a central shaft that is prone to material buildup. Cage-shaped reactors, on the other hand, have a larger surface area, higher film formation efficiency, and no central shaft connection, thus eliminating the issue of material buildup. Our company uses an independently developed cage-shaped reactor, which boasts excellent film formation effects and high polymerization efficiency, capable of shortening the reaction time.
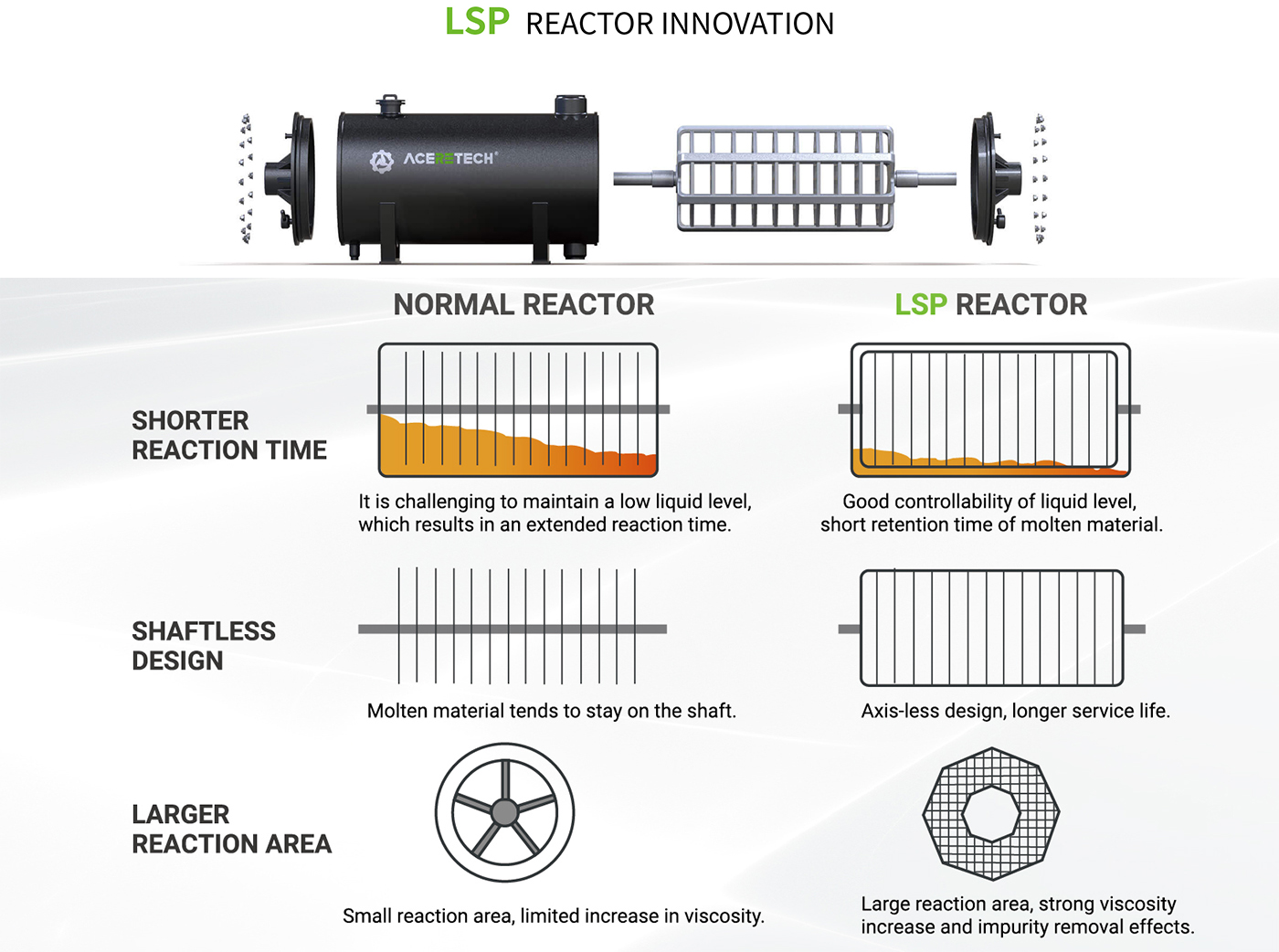
Non-shaft design
The unique shaftless design makes the melt filming reaction smoother, avoiding the risk of material accumulation.
Larger reaction area
The larger reaction area has better decontamination efficiency, better IV-increase effect, and achieve higher purity after reaction.
Shorter reaction time
Innovative mesh design allows smoother melt flow, which makes the liquid level control more stable and can be controlled at a very low level, allowing the melt reaction time to be shortened and the end product color to be better.