Good news! Another battery isolation film recycling granulation production line has been perfectly accepted in China!
With the rapid development of the new energy sector, the demand for efficient lithium battery separator film recycling solutions has never been greater. At ACERETECH MACHINERY, we specialize in providing advanced granulation and recycling technology tailored to the unique challenges of these high-polymer materials.
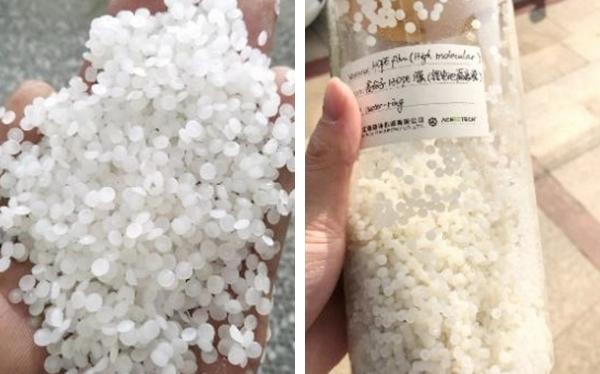
Challenges in Lithium Battery Separator Film Recycling
Unlike conventional plastic films, lithium battery separator films vary significantly in composition, especially between oil-containing and non-oil films. In some cases, dry films may also contain residual oil, which is not visible to the naked eye. These materials can reach thicknesses of up to 2mm, requiring specialized processing solutions.
ACERETECH’s Recycling Approach
* Dry Film Processing: We utilize an integrated shredding and granulation system for seamless, continuous processing. Due to the high tensile strength of these films, pre-treatment is essential—without it, granulators may struggle to cut the material, leading to unstable extrusion current or even machine shutdowns.
* Oil Film Processing: The most critical challenge in recycling oil-containing films is effective oil separation. Once oil collection is properly managed, the granulation process becomes highly efficient. Additionally, oil films exhibit better flowability than dry films, resulting in a noticeable increase in final output.
So far, we have provided over 12 lithium battery separator recycling and granulation lines to more than 5 customers.
With our proven expertise and innovative solutions, ACERETECH is committed to helping you optimize your lithium battery separator film recycling process.
1. Pre-shredding: Due to the high tensile strength of these films, pre-treatment is essential—without it, granulators may struggle to cut the material, leading to unstable extrusion current or even machine shutdowns.
2. Compacting: Rotary blades on the knife-disk and fixed blades on the wall cut film into small flakes. Heat which caused by high speed friction pre-heats and dries the film and make them shrink. Arc-shaped plates guide the material down and into the extruder under the centrifugal force of knife disk. Also, we can remove most the oil in the compactor by the centrifugal force when we recycle oil film. Ofcourse, we will special design the compactor to let the oil be collected outside the compactor.This combined process of size-reduction, pre-heating and compacting enables stable and effective feeding for small bulk density plastics.
3. Filtration:Due to the low fluidity of the film, we chose a plate type screen changer
4. Water-ring pelletizing system: Cutting speed is automatically adjusted according to melt pressure at the die head to ensure even granules.Pressure of blade onto the die is automatically adjusted to ensure uniform cutting force by high precision pressure sensor.
If you are interested in learning more about our solutions, feel free to reach out to us—we would be happy to discuss how we can assist your business.